The growing demand for AMT precision parts has transformed manufacturing landscapes across industries, creating new possibilities for products that require exacting tolerances and consistent quality. These meticulously engineered components—often invisible to end users but critical to performance—represent the hidden architecture behind everything from medical devices to aerospace systems to next-generation electronics. As global supply chains evolve and manufacturing technologies advance, the precision parts sector stands at the intersection of technical innovation and industrial necessity.
The Anatomy of Excellence: Understanding Precision Manufacturing
When we examine what truly constitutes precision in manufacturing, we confront a world measured in microns and governed by mathematical absolutes. Modern AMT precision components regularly maintain tolerances as tight as ±0.0001 inches—approximately 1/10 the width of a human hair. This level of exactitude doesn’t happen by accident or through conventional manufacturing approaches.
The creation of these components involves several critical technologies:
· Computer Numerical Control (CNC) machining with advanced 5-axis capabilities
· Electrical Discharge Machining (EDM) for creating complex geometries in hardened materials
· Precision grinding and honing processes for achieving superior surface finishes
· Advanced metrology systems utilizing laser measurement and machine vision
· Automated quality control protocols that maintain consistency across production runs
“The global market for high-precision components is projected to reach USD 467 billion by 2028, with the most significant growth occurring in medical, aerospace, and electronics sectors.” – International Manufacturing Technology Review, 2023
Beyond Buzzwords: The True Value of Precision
Precision isn’t merely a technical specification—it represents fundamental value across the product lifecycle. When components fit together with minimal variation, assemblies perform more reliably, last longer, and require less maintenance. This relationship between precision and performance creates ripple effects throughout entire industrial ecosystems.
Consider the medical device industry, where precision parts literally save lives. Implantable devices, surgical instruments, and diagnostic equipment all depend on components manufactured to exacting standards. A cardiac pacemaker lead with dimensional variations could fail prematurely; an improperly machined surgical instrument might not function correctly during a critical procedure.
In aerospace applications, precision directly impacts safety, efficiency, and environmental impact. Engine components manufactured with tight tolerances improve fuel efficiency, reduce emissions, and extend service intervals. The economic and environmental benefits compound over thousands of flight hours and millions of passengers.
The Technology Behind the Tolerance
The manufacturing processes that create today’s most advanced precision parts bear little resemblance to traditional machining operations. Modern production facilities function more like laboratories than factories, with controlled environments, sophisticated monitoring systems, and production equipment that costs millions.
The technological progression has been relentless:
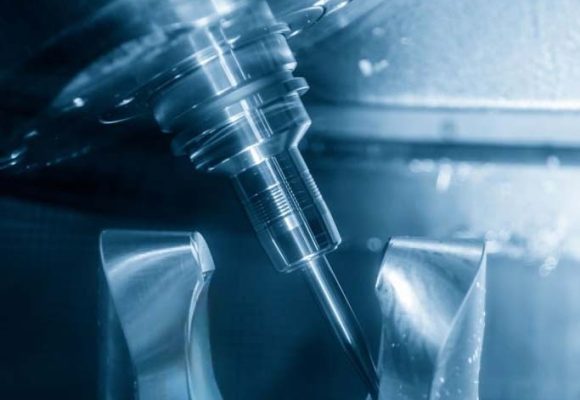
· Digital twin modeling that simulates manufacturing processes before material is cut
· Artificial intelligence systems that optimize cutting paths and predict tool wear
· Advanced materials science creating cutting tools capable of maintaining edge integrity through thousands of operations
· In-process measurement systems that provide real-time feedback and adjustments
· Thermal stability systems that compensate for dimensional changes due to heat
These technologies don’t merely improve existing processes—they fundamentally redefine what’s possible in component manufacturing.
The Human Element in a Precision World
Despite technological advances, the human element remains irreplaceable in precision manufacturing. Behind every sophisticated machine stands an operator whose experience and intuition complement computational precision. The most advanced facilities maintain apprenticeship programs where knowledge transfers from veteran machinists to new generations, preserving craft knowledge while embracing technological evolution.
This human-technology partnership creates resilience within manufacturing systems. When unexpected challenges arise—unusual material characteristics, tool performance issues, or novel geometrical requirements—experienced technicians provide adaptability that purely automated systems cannot match.
“Our studies indicate that facilities combining human expertise with advanced automation achieve 23% higher first-pass yield rates than fully automated competitors.” – Manufacturing Excellence Institute, 2022
Global Competition and Local Excellence
The competitive landscape for precision manufacturing has globalized dramatically, yet regional excellence persists. While high-volume, lower-precision production has shifted predominantly to emerging economies, the most demanding precision applications often remain anchored in traditional manufacturing centers where multi-generational expertise clusters.
This pattern creates interesting collaborative networks where design may occur in one region, while different manufacturing stages distribute according to specialized capabilities:
· Prototype development in innovation hubs with rapid iteration capabilities
· Complex component manufacturing in precision centers of excellence
· Assembly operations in locations optimized for logistics and labor
· Testing and validation in facilities with specialized certification capabilities
The most successful precision manufacturers navigate this distributed landscape while maintaining consistent quality and intellectual property protection.
The Economics of Exactitude
The financial realities of precision manufacturing often challenge conventional business models. The substantial capital investment required for state-of-the-art equipment creates high barriers to entry. Machine tools capable of achieving the most demanding tolerances can cost upwards of £1 million, requiring careful utilization strategies to justify the investment.
Meanwhile, the skilled workforce needed to operate these systems commands premium compensation, further pressuring margins. Successful precision manufacturers respond with several approaches:
· Focusing on industries where precision directly correlates with higher component value
· Developing proprietary processes that competitors cannot easily replicate
· Establishing long-term partnerships with customers who recognize quality value beyond unit price
· Creating intellectual property around manufacturing processes themselves, not just end products
· Implementing lean methodologies that maximize equipment utilization and minimize waste
The Technological Horizon
Future developments in precision manufacturing will likely blur traditional boundaries between discrete manufacturing processes. Hybrid systems combining additive and subtractive technologies already show promise for creating geometries impossible through conventional methods alone. Meanwhile, advances in material science—including metallic glasses, ceramic-metal composites, and programmable materials—will demand new approaches to precision fabrication.
Emerging technologies poised to transform precision manufacturing include:
· Quantum sensing systems capable of detecting atomic-level variations in material structure
· Bio-inspired manufacturing approaches that mimic natural growth processes
· Ambient intelligence systems that continuously optimize production environments
· Molecularly precise manufacturing techniques approaching theoretical limits of material manipulation
· Self-healing production systems that compensate for tool wear and environmental variations
Conclusion
The evolution of manufacturing technology continues to redefine what’s possible in component production. As industry demands increase and tolerances tighten further, the symbiotic relationship between sophisticated machinery and skilled operators will remain central to creating the next generation of precision components. The manufacturers who navigate this complex landscape—balancing capital investment, workforce development, and technological adoption—will define excellence in the precision economy. For companies building tomorrow’s most demanding products, the path to reliability, efficiency, and competitive advantage will increasingly run through partnerships with suppliers specializing in AMT precision parts.